Now that I have been able to bend some wood with the new iron, I wondered what the temperature really is when it is running. I also want to know how long I have to wait for it to come up to temp. Guessing is all well and good, but my engineering background makes me want to know the numbers.
According to what I have read, the ideal temperature for bending wood is around 400° F. I want to see if the pipe gets that hot, and how long it takes to get there.
So I bought this Infrared Thermometer at a Big Box Home Improvement Store (BBHIS) for about $40. They claim that it can measure temperatures from -40° F to 1076° F by measuring the radiation from the surface of the object.

My new Toy
This is really cool. When you pull the trigger, it shows a neat laser target on the surface that it is measuring.
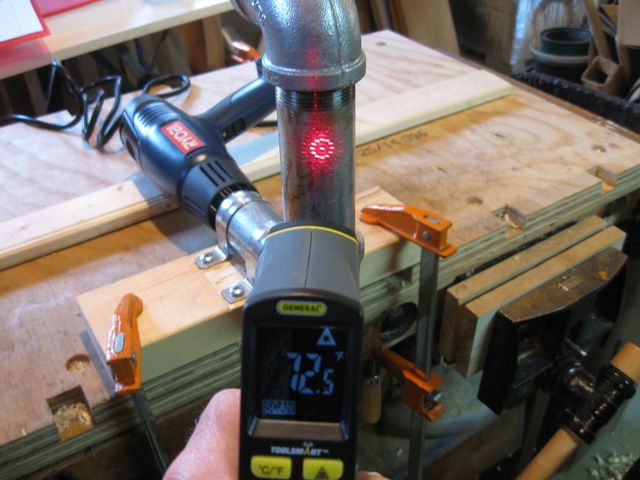
Measuring the Temperature of the Pipe
The display is showing the temperature of the pipe before I turned on the heat gun. A thermometer I have hanging on the wall said that it was 68° in there. So this is close.
Here is the setup. My plan was to set the heat gun to one of its air temperature settings, then measure the temperature of the pipe once each minute until it stabilizes.

The Setup
You can't see it in the photo, but that plastic clock has a second hand on it. Each time the second hand pointed at the 12 I took a measurement of the pipe temperature and wrote it on the clipboard.
I started at the 500° setting since it is clear that the pipe will not heat up to 400° when the air temperature is set to 200°. So there was little point in using that setting.

Set to 500°
I took readings every minute for 20 minutes. The thermometer is a bit finicky. The temperature jumps around all over the place when I point it at the pipe. It does finally find a maximum temperature as it jumps around. I found that I had to watch the numbers and pick the highest temperature that I saw. I figured that a low temperature would come from a misalignment of the sensor with the radiating pipe, but the only thing that could cause a high temperature to register would be the actual radiation from the pipe. So I scanned the pipe and wrote down the highest temperature that I saw.
After the 20 minutes was up I took my practice wood and tried it out on the pipe.
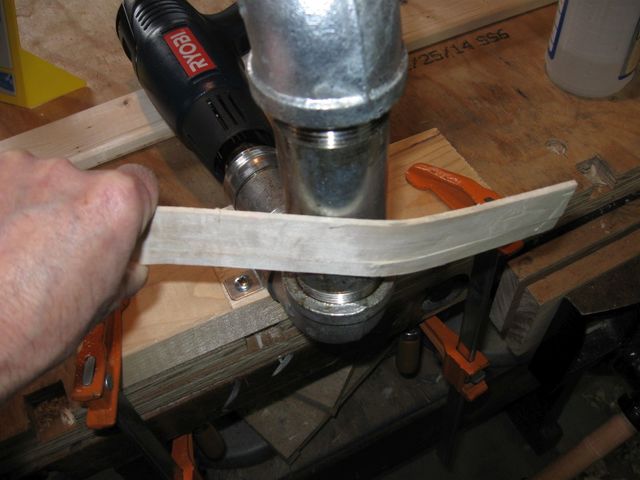
Bending the Practice Wood Again
It did bend, but very slowly. There also seems to be some splitting on the outside of the wood where I pressed it against the iron.

There is Some Splitting There
But it did bend. Here a photo of the additional bend that I put in the wood.

A New Bend in the Wood
I let the pipe cool down completely to room temperature before doing the next test. This time, I set the air temperature to 800° F.
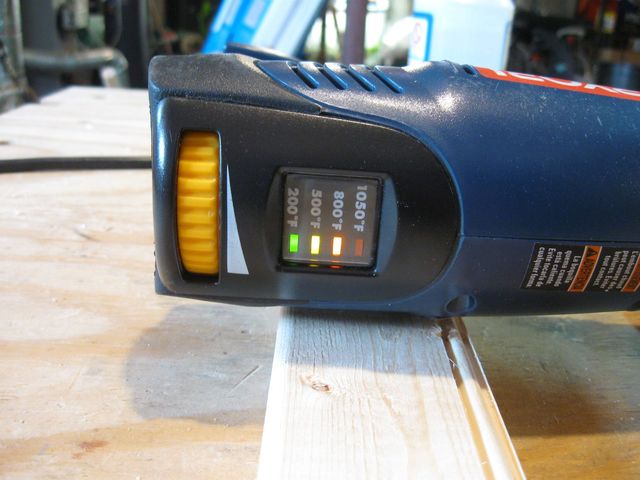
Set to 800°
Once again, I took a measurement every minute for 20 minutes and wrote the number down in the table.
After the 20 minutes was up, I tried bending the wood again. I was running out of length to bend, so I tried to unbend one of the curves that I had bent previously. That was to see if I could correct mistakes where I had bent the wood in too sharp of a curve.

Unbending one of the Previous Bends
Again, at this setting the wood would bend. It was a little easier than it was at the lower setting, and I didn't see any splitting on the opposite side. Here is a photo of the end of the wood where I took out the bends.
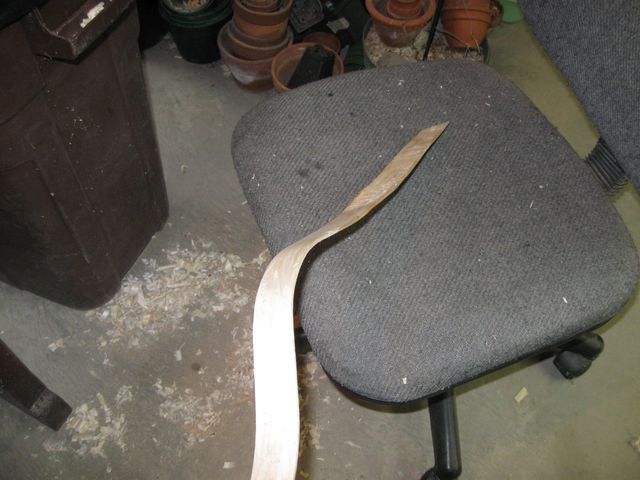
That End Used to Have a Bend in It
I was extra generous wetting down the wood with the sprayer this time to see if it would make more steam and then bend easier. Instead, I got the dreaded Cupping. I have read that you do not want to soak the wood before bending it on the iron because too much water in the wood can cause it to cup. Check it out.
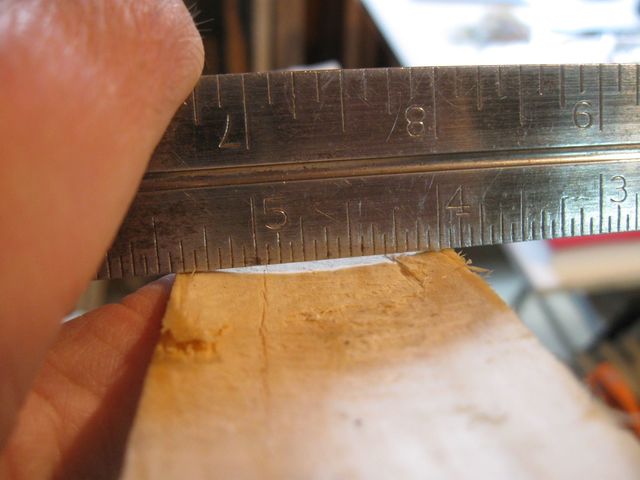
That Wood is Cupped
I will have to remember to be judicious with the spritzing of the wood when I am actually bending the real sides.
I let the iron cool down to room temperature again and then started my last test with the heat gun set to 1050° F

Set at 1050° F
I ran the test for 20 minutes like the other tests and then tried to bend the wood again. This was the setting that I used when I first attempted to bend.
I tested my ability to unbend some of the curves again.
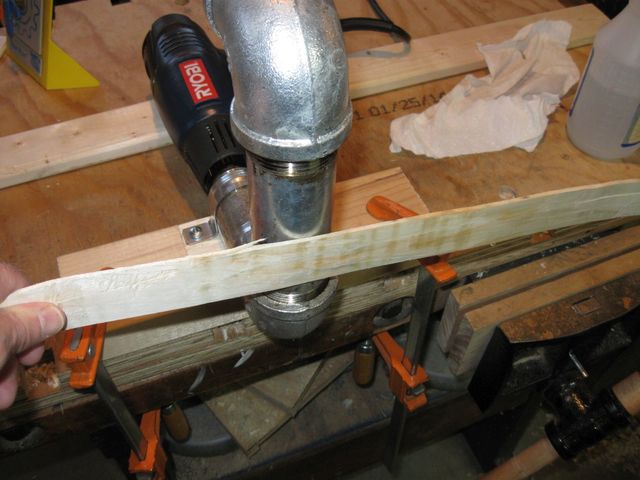
Unbending The Previous Curves Again
At this setting, the wood worked the same way it did the first time I tried it. I held it gently against the iron. The feeling went like this. Springy.... springy..... springy.... Ahhhhh.... it softens and wraps around the iron. Move over 1/4".... springy.... springy.... springy.... Ahhhhhh... it softens and wraps around the iron. I kept doing that until the curves came out of the wood.
There is a bit of timing involved, and figuring out how much pressure to apply, but none of it is difficult. I did not have to push hard on it. I straightened out all of the curves in that board.
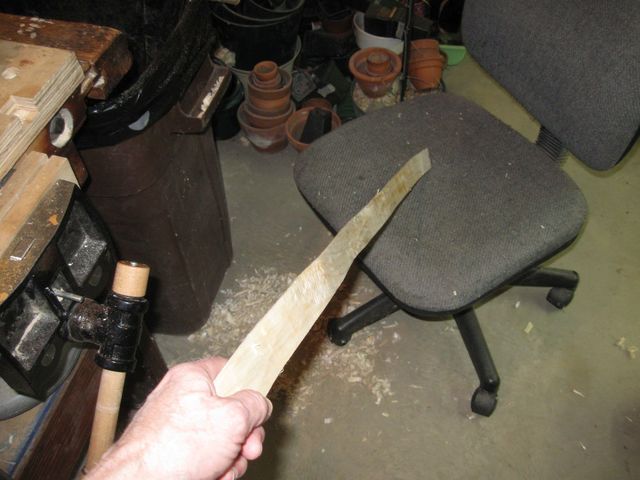
The Board is Mostly Straight Again
That isn't ramrod straight, but it is straight enough for me to presume that I will be able to adjust the shape of a side to fit a template without a lot of difficulty.
Just for grins, I thought I would measure some of the surrounding surfaces to see what all that heat is doing to the area. So with the heat still cranking, I pointed the thermometer to some different areas. The surface of the heat gun itself is just about body temp.

Body Temp. No Danger There
I originally had a concern that the temperature of the lower pipe might scorch the wood platform I have screwed it to, or even set fire to it. So I measured the temperature of the wood under the iron.

That is Certainly Not Going to Combust
I measured the top end of the pipe, where the air is coming out.
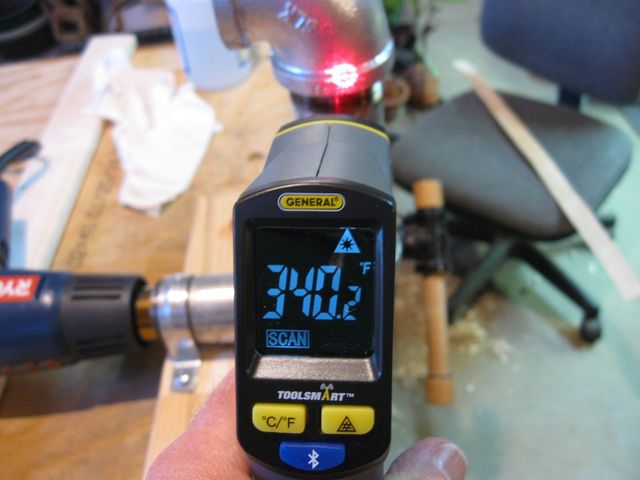
That's Hot
The thermometer, while a bit finicky, has worked fairly well once I got the hang of how to use it.
Here is the data that I captured while I was doing the test.
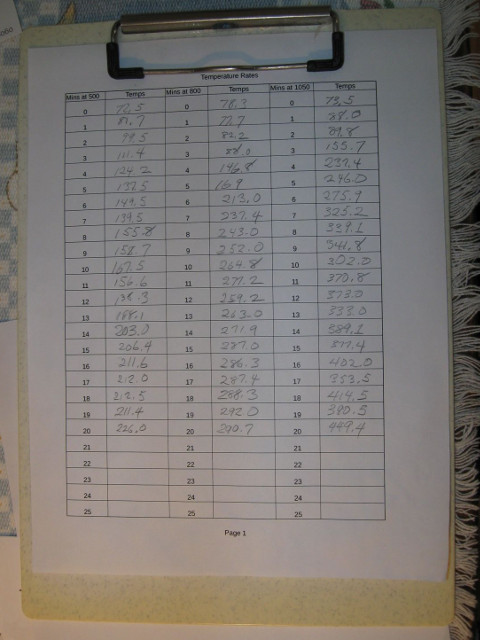
The Temperature Data
OK, here's the data in a form where you might actually be able to read it.
Mins at 500 | Temps at 500 | Mins at 800 | Temps at 800 | Mins at 1050 | Temps at 1050 |
---|---|---|---|---|---|
0 | 72.5 | 0 | 78.3 | 0 | 73.5 |
1 | 81.7 | 1 | 77.7 | 1 | 88 |
2 | 99.5 | 2 | 82.2 | 2 | 89.8 |
3 | 111.4 | 3 | 88 | 3 | 155.7 |
4 | 124.2 | 4 | 146.8 | 4 | 237.4 |
5 | 137.5 | 5 | 169 | 5 | 246 |
6 | 149.5 | 6 | 213 | 6 | 275.9 |
7 | 139.5 | 7 | 237.4 | 7 | 325.2 |
8 | 155.8 | 8 | 243 | 8 | 339.1 |
9 | 158.7 | 9 | 252 | 9 | 341.8 |
10 | 167.5 | 10 | 264.8 | 10 | 302 |
11 | 156.6 | 11 | 277.2 | 11 | 370.8 |
12 | 138.3 | 12 | 259.2 | 12 | 373 |
13 | 188.1 | 13 | 263 | 13 | 333 |
14 | 203 | 14 | 271.9 | 14 | 389.1 |
15 | 206.4 | 15 | 287 | 15 | 377.4 |
16 | 211.6 | 16 | 286.3 | 16 | 402 |
17 | 212 | 17 | 287.4 | 17 | 353.5 |
18 | 212.5 | 18 | 288.3 | 18 | 414.5 |
19 | 211.4 | 19 | 292 | 19 | 390.5 |
20 | 226 | 20 | 290.7 | 20 | 449.4 |
The Temperature Data in Readable Form
I also plotted the data to make it easier to see what is going on at the different settings.

The Temperature Data Plotted
There are quite a few flyers in the data because the thermometer was finicky about where I was pointing it and how I was using it. But the trends are there.
Set at 500° | I think the last data point is a flyer. It looks like it topped out at just over 200° somewhere around 17 minutes. |
Set at 800° | The data looks more regular. It topped out at just under 300°, also at about 17 minutes. |
Set at 1050° | These numbers are all over the place. But there is a trend up. It looks like the temperature was still going up when I quit. |
Observations
So I think that when I use it, I might want to set the heat gun to the maximum, 1050°, let it go for about 15 minutes to warm up, then turn it down to 800° to maintain the temperature while I bend the wood. The wood bent somewhat at all the temperatures, so that plan will probably work out even if it cools off a bit while I am bending.